Precision Engineering in Limited Space: Successful Slewing Bearing Seating Face Machining
We are proud to introduce our low-profile, circular self-leveling milling machine, specifically designed and built for operations in confined headspace conditions. This innovative solution enables clients to lift the crane’s superstructure rather than completely removing it and placing it on the ground. By allowing machining of both bearing seating faces—on the carriage and the superstructure—in a single setup, our machine significantly reduces time and costs when replacing slewing bearings.
In January 2025, we successfully delivered this advanced machine, and after the Lunar New Year, our team travelled to Penang to commence the project. Despite the challenging low-headroom conditions, our skilled team achieved an exceptional surface flatness runout of ≤0.15mm on a 3-meter diameter slewing bearing surfaces. Their unwavering dedication and expertise ensured that the project was completed ahead of schedule, with full on-site support.
A huge thank you to our team for their hard work, precision, and commitment to excellence—especially while working in such physically demanding conditions. Well done, everyone!

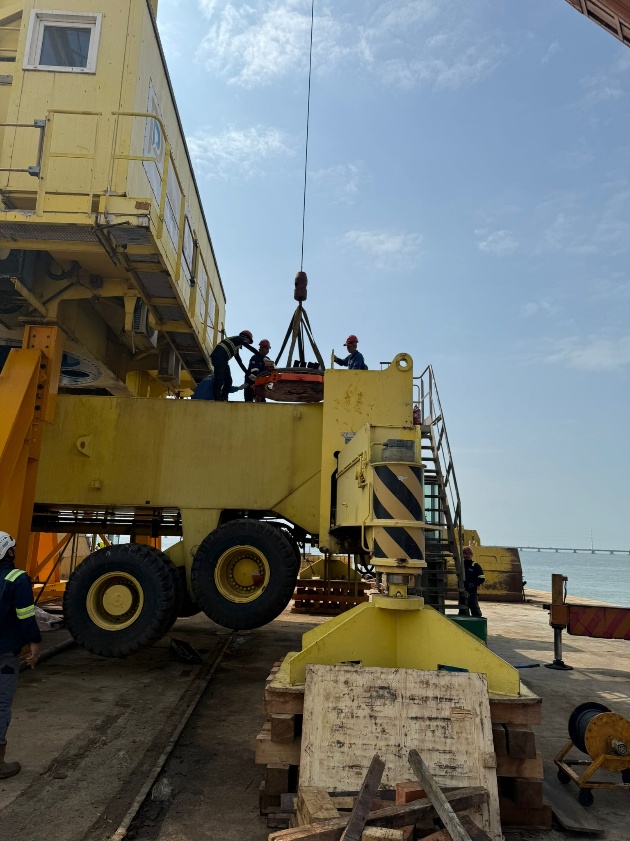
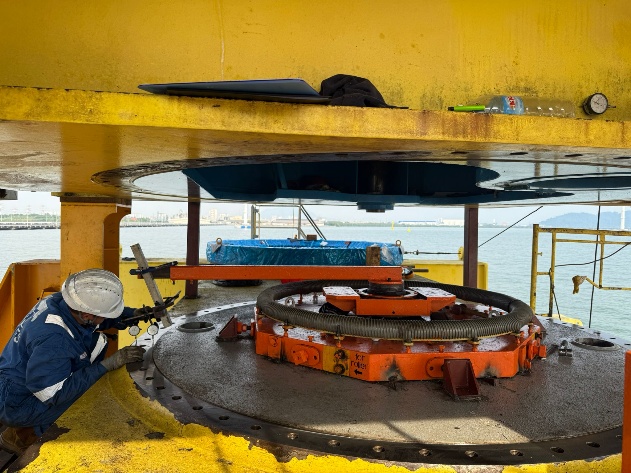
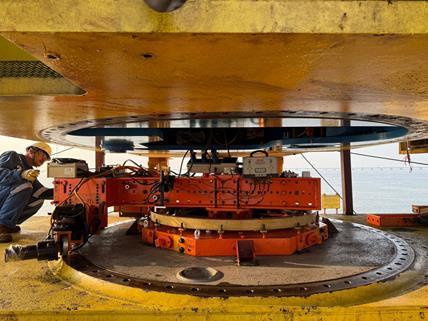