CNC Machining
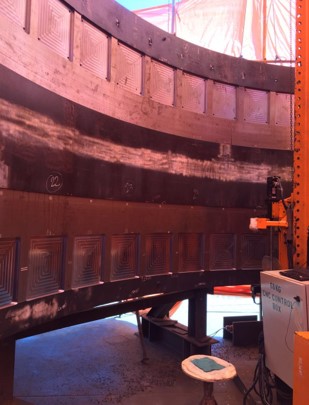
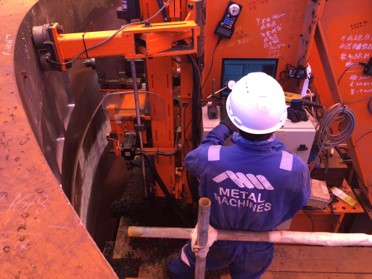
The primary objective to develop CNC milling and boring capabilities was to provide higher precision and repeatability to critical components such as steam turbine casing. As more clients realise the cost saving of insitu machining, large components which used to be machined in workshops are preferred to be conducted at site as in-situ solutions are available now. Other than the steam turbine casing boring, cnc milling capability was used to machine the guide vane of hydroturbine at site as well as journal bearing seating pads for large size ferris wheel etc.Other than the 3 axis of cnc machining, the engineering teams are also exploring the usage of 4 to 5 axis cnc machining to provide further options for our clients.